Heat is an instigator, in many cases speeding up chemical reactions. It’s why food is stored at cold temperatures to keep fresh. In manufacturing settings where speed is key, heating things up can increase efficiency, but sometimes the application of heat is not precise enough and can encourage unwanted reactions. Penn State Associate Professor of Chemistry Ben Lear is studying how to apply heat to chemical reactions in a much more targeted way.
“The traditional ways we apply heat to reactions are grossly mismatched to the scale of the tiny molecules used in a chemical reaction,” said Lear. “The difference in scale could be a billionfold or more. It could be too much heat, over too large of an area, lasting too long. My lab thinks about ways to apply heat this is more targeted to the molecular scale.”
Lear works with nanoparticles—tiny particles more than 7,000 times smaller than the width of a human hair—that absorb light. When he shines a focused light on a particle, the particle absorbs the light and converts it into heat. The heat then diffuses out of the particle and can be used to drive a chemical reaction. This kind of focused light can increase the temperature of particle by 1,000 degrees Celsius or more.
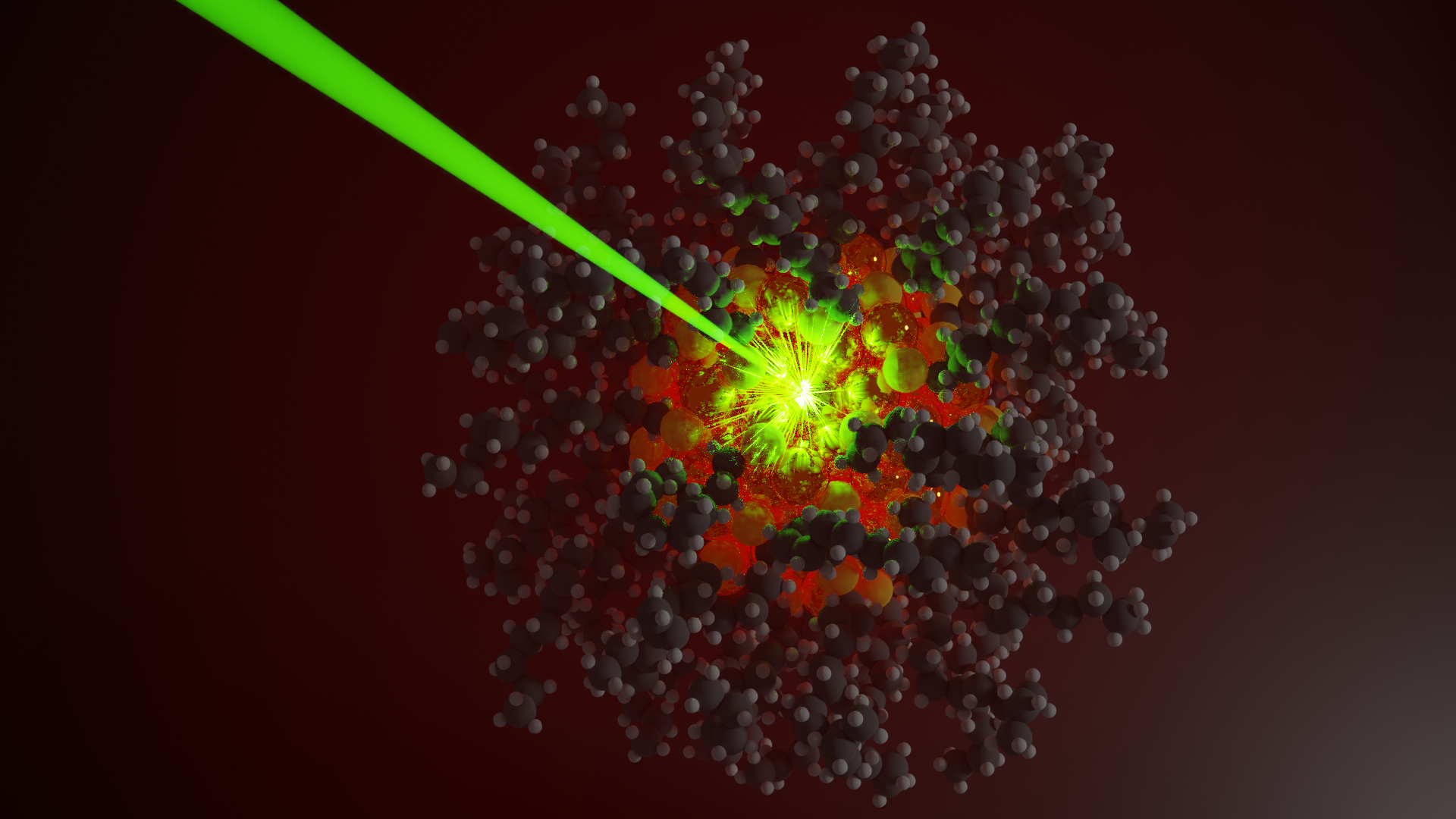
“If you took a box and heated it to 1,000 degrees, it would probably catch on fire and turn into charcoal,” said Lear. “That doesn’t happen here, which tells us this system is functioning differently. My lab has demonstrated that these localized increases in temperatures, even at such extremes, are able to cleanly drive conventional organic chemical reactions. Now we are exploring how to tune this effect to promote desired reactions, including those used in additive manufacturing.”
Additive manufacturing processes, including 3D printing, build complex materials from the ground up, layer by layer. Each new layer is deposited on and adhered to the previous layer, sometimes in a partially melted from that needs to cure, or harden.
A number of materials have been used in additive manufacturing, including metal, ceramics, plastics, and some polymers—molecules or macromolecules with repeating subunits.
“Some types of polymers are well represented in additive manufacturing,” said Lear. “Another type, called thermosetting polymers, are commonly used in other areas of manufacturing, for example to make rubber, two-part epoxy, and protective coatings for cars and other metals. But thermosetting polymers are not commonly used in additive manufacturing because they require heat to cure, and traditional ways to apply heat make it hard to control the curing process.”
In 2018, Lear was awarded a Lab Bench to Commercialization (LB2C) grant to help translate his research about targeted heat application to additive manufacturing with thermosetting polymers. The grant, co-funded by the Eberly College of Science, Invent Penn State, the Penn State Research Foundation, and the University's Fund for Innovation, provides $75,000 to promote translational research, with the primary aim of moving technologies towards commercialization.
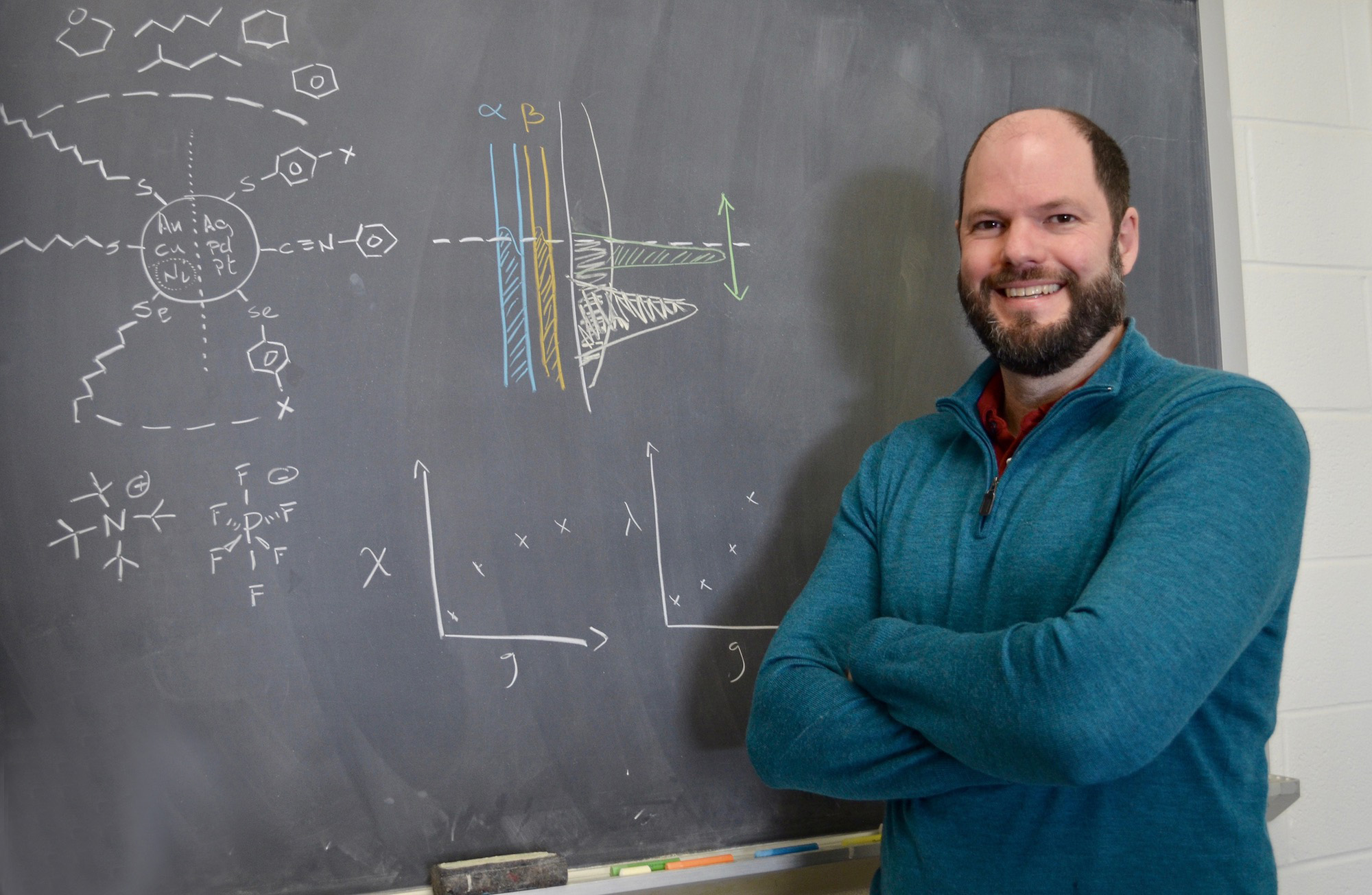
With support from the LB2C grant, Lear and his lab were able to build a printer for thermosetting polymers. The printer allows Lear to control where and when the material is deposited, and where and how quickly the materials cure. This also helps him to stop and start reactions much more efficiently.
“For something like two-part epoxy, for example as a coating for your garage floor, you mix the two ingredients, apply it, and then you have to wait hours for it to cure before you can use it or perform the next step,” said Lear. “Here, we mix the light-absorbing nanoparticles into the components and can cure the resulting polymer ‘on-demand’; just by shining a light, the material cures almost instantly. People have used on-demand curing in other manufacturing processes, but now we can bring it to additive manufacturing of thermally cured polymers.”
Lear and his team are now seeking additional funds to refine their printer, and he and recent doctoral student Joseph Fortenbaugh founded Actinic to pursue this work. Fortenbaugh has been awarded a prestigious two-year Innovation Crossroads fellowship from the Oak Ridge National Laboratory to further develop the technology. The ultimate goal is to demonstrate a commercially viable printer and polymer formulations—somewhat like recipes—for it.
“The polymers we are targeting are already commercially relevant—you can buy them at the store,” said Lear. “But it takes the technology and a certain amount of know-how to disperse these light-absorbing particles inside the mixture of chemicals that will eventually form the polymer that you’re trying to cure, as well as to build an effective printer for these mixtures. But being able to use on-demand curing with these polymers could open up a lot of new opportunities for materials.”
To learn more about this grant program or the described technology, please contact the Eberly College of Science Office for Innovation at innovation@science.psu.edu or 814-867-6287.