A note from the guest editor:
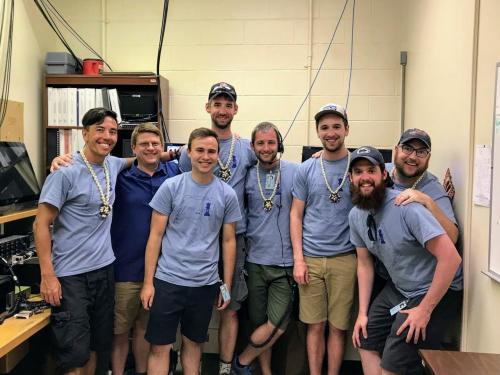
What if you need to make a first-of-its-kind measurement at a previously unfathomable accuracy? Well, then you need to have a really good idea of what it would take to make the measurement, and you also need to build it and test it. Randy McEntaffer, in the Department of Astronomy and Astrophysics, studies major events in the universe by analyzing precise X-ray wavelengths collected by spectrographs that he builds. Ironically, to build this instrument to study incomprehensibly big events in the universe, he needs to fabricate incomprehensibly small components. As you read Randy’s story, please note the role that one of our core instrumentation facilities, the Materials Research Institute’s Nanofabrication Laboratory, played in his recruitment to Penn State. His recruitment, however, is not unique. State-of-the-art instrumentation facilities with highly skilled technical staff to assist and train students and faculty are magnets that attract outstanding faculty. The majority of these facilities charge a user fee that recovers the cost of the staff, the maintenance contracts, and some depreciation (pro t is not permitted). Faculty pay these fees from their grants, and many companies sponsor faculty research that takes advantage of the facilities. To test his X-ray spectrographs, Randy needs to launch them into sub-orbital space, collect the X-ray data, and write the software to analyze the data. Undergraduate students are involved in all phases of the project. They assist in the nanofabrication of diffraction gratings, assemble the spectrograph in the body of the rocket, write code for the data analysis, and assist with the rocket launch and recovery. Randy’s students can also sometimes be found exiting the Millennium Science Complex on weekdays, evenings, and weekends. This is a wonderful example of how the University’s investment into instrumentation helps place it at the forefront of research, attracting leading edge researchers like Randy, and giving graduate and undergraduate students hands on experience in the research and discovery continuum. Andy Stephenson
X-ray Spectrographs
To state the obvious, the universe is big. Incomprehensively big. And old. Nearly 14 billion years old. We’ve been curious about what’s going on out there for probably the entirety of human existence—a mere couple hundred thousand years at most. That curiosity is not purely academic; understanding our universe helps us understand our place in it, drives our knowledge of the basic laws of nature, and pushes the technological advances that will lead us into the future.
Almost everything that we know about the universe so far, we’ve learned from electromagnetic radiation—photons that travel through space-time at the speed of light carrying varying amounts of energy while behaving simultaneously like particles and waves.
Until extremely recently, our understanding of the universe was based entirely on information from a very small fraction of the electromagnetic spectrum: visible light. Under normal circumstances the light we can see with our eyes looks white, but we know that a prism or droplets of water in the sky can separate that light into the colors of the rainbow: red, orange, yellow, green, blue, indigo, and violet. The different colors of visible light represent different wavelengths, frequencies, and energies. Red is at the low energy end with a longer wavelength and lower frequency than violet at the high end. But, the electromagnetic spectrum extends far beyond this narrow visible band in both directions, a fact that was only discovered about 200 years ago.
Below red there’s infrared and then microwaves and radio waves. Above violet there’s ultraviolet, X-rays, and gamma rays. While visible light can tell us certain types of information about the universe—How far away is a star? How big is it?—other forms of electromagnetic radiation can carry other types of information. To get at that information we must develop the technology to let us “see” beyond what we can see with our eyes.
“Our lab is interested in what we can learn about our universe from diffuse, low energy—or ‘soft’—X- rays,” said Randall McEntaffer, professor of astronomy and astrophysics and of physics. “Stars, supernova remnants, black holes, and active galactic nuclei all can emit X-rays that carry with them information about their sources and what they encounter on their journey. To be able to answer more and more sophisticated questions about these astrophysical phenomena, we need to design and build more and more sophisticated tools to help us interpret the information that these X-rays carry.”
Creating these tools requires innovative researchers with access to immense resources and cutting-edge facilities. The Eberly College of Science at Penn State is one of only a handful of places where this can be done.
Science drives innovation
If an astronomer wants to answer questions about the universe beyond what we can see with our eyes—even if magnified by looking through a telescope—they need to create tools to get that information. X-rays can carry information about the elements that compose their sources, the amount of heat involved in their creation, and more. To extract that information from the mass of X-rays hurtling through space we need precise instruments. Designing, building, and testing the new technology that will allow that information to be extracted and drive the science of X-ray astronomy into the future is what McEntaffer and his team of research faculty, undergraduates, and graduate students do.
“It’s not necessarily the first thing that people think of when they think of astronomers,” said McEntaffer. “But a big part of what we do is technology development. The science that we want to do forces us to come up with new and innovative ways to gather and evaluate the data we need.”
Penn State, in fact, has a long history of leading X-ray astronomy with its involvement in NASA’s Swift and Chandra X-ray observatories. These large-scale, incredibly expensive NASA satellites have been the workhorses in X-ray astronomy for two decades, but the technology on these satellites, launched in 1995 and 1999 respectively, is prime to be replaced with new, more efficient and precise instruments.
The science therefore drives the development of technology. Astronomers like McEntaffer are pushing the boundaries of what our instruments can do, but they need the facilities that allow them to build and test these complex instruments and they need collaborators whose expertise compliments their own, creating an environment for developing new technology with the fewest hurdles to overcome. Penn State has both. McEntaffer’s group collaborates with Abe Falcone and David Burrows in the Department of Astronomy and Astrophysics, who design and build the detectors that are an integral part of McEntaffer’s X-ray instrument. He also only has a short walk across campus to the Nanofabrication Laboratory, which is part of the Penn State’s Materials Research Institute and is one of the few places in the world with the technology and expertise to fabricate the instruments.
Splitting up the X-rays
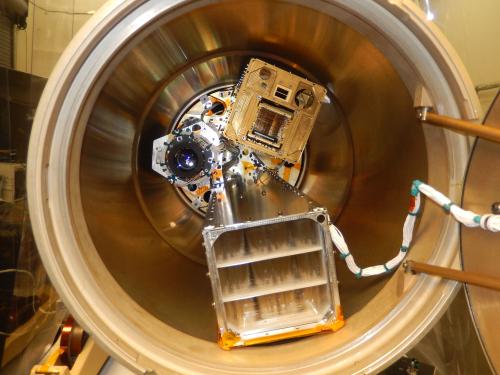
Just like visible light, X-rays come in a range of wavelengths and energies. The low-energy, soft X-rays that McEntaffer’s group is interested in range in energy from about 100 electron volts (eV)— or 0.1 kilo-electron volts (keV)—to about 10 keV. For comparison, the visible light spectrum falls entirely under 10 eV. They are particularly interested in X-rays in an even narrower range—from about 0.2 to 2 keV—which are emitted when atoms of the most abundant elements in the universe transition from one state to another and therefore carry information about the composition of astronomical objects and events.
When a cataclysmic event—like a supernova, for example—occurs in space, the energy and radiation released can ionize the atoms that compose the exploding star and the atoms in the surrounding interstellar space, causing them to transition to a new state by losing electrons. When this ionization occurs, the atoms emit X-rays of a signature energy in the soft X-ray range. A particular ion of oxygen, for example, will emit an X-ray with a specific wavelength and amount of energy. If we can detect an X-ray with that specific energy, we know that particular oxygen ion was present in the X-ray’s source. The amount of that particular X-ray we detect can tell us about the abundance of the ion, and the relative amounts of X-rays from other ions can give us information about the physics of the event that created them.
“To get this information we need to be able separate out and detect X-rays of various energies in a way that is sort of analogous to splitting visible light with a prism,” said McEntaffer. “Of course, X-rays behave differently than visible light and we need to be able to make incredibly fine distinctions. So, in order to pick out the information carried by these X-rays, we need to develop the tools that can do this.”
McEntaffer’s group designs, builds, and tests X-ray grating spectrographs. To oversimplify, these spectrographs have two main components: the ‘gratings,’ which separate the X-rays by wavelength or energy level; and a detector, not unlike the sensor in the camera of your smartphone, that can detect even a single photon of an X-ray and translate that energy into information that we can use.
The X-ray spectrographs work by funneling the X-rays from a region in space through the gratings. These gratings are incredibly precise instruments. The gratings McEntaffer designs require a range of about 6,200 to 6,400 lines to be etched per millimeter across a plate of silicon. The angles of the etched lines must be precise down to the level of an angstrom, a unit of length equal to one hundred-millionth of a centimeter. Creating these gratings requires an institutional-level facility with massively expensive equipment that is beyond the means of just about any single laboratory. Penn State has just such a facility in the Nanofabrication Laboratory that is part of the Materials Research Institute on campus. Access to this facility and its expert staff helped motivate McEntaffer’s move to Penn State.
McEntaffer’s group has been building and testing this new generation of more-efficient X-ray spectrographs since he was a professor at the University of Iowa. The ultimate goal is to produce an X-ray spectrograph that can be integrated into NASA’s next large-scale astronomical satellite, something on the scale of the Swift or Chandra satellites. But first, McEntaffer must demonstrate that his instrument works and that it can survive the rigors of being launched into space. Doing this got easier when McEntaffer made the move to Penn State.
“When I was at Iowa, I was farming out the fabrication process to many other facilities, including Penn State,” said McEntaffer. “Trying to piece that all together is really difficult and time consuming to do; what should take weeks, takes months. Penn State’s Nanofabrication Laboratory has basically every tool that I need in one location.”
Nanofab is a mega-draw
Why come to Penn State from Iowa? When the instruments you need to build for your research can only be built in a handful of facilities in the world and one of them is here on campus, the decision is easy. The Nanofabrication Laboratory at Penn State houses world-class instruments for deposition, etching, lithography, and material modi cation and characterization. The wide variety of available processes give Penn State faculty and students, as well as users from outside the university, the ability and flexibility to develop and fabricate many types of novel devices.
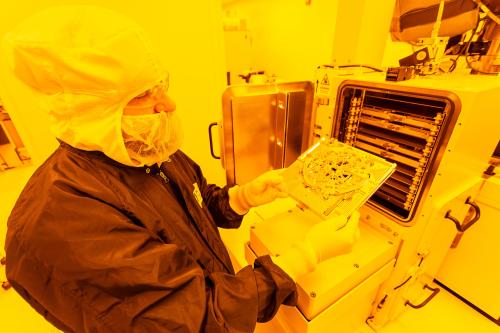
“The nanofab lab evolved out of a bunch of separate labs and clean-room facilities that previously existed on campus,” said Chad Eichfeld, director of operations for the Nanofabrication Laboratory. “When the Millennium Science Complex was built, all of these labs were pulled together to form what we are now.”
McEntaffer utilizes electron-beam lithography at the nanofab lab to create the gratings for his X-ray spectrographs. A wafer of silicon is coated with a “resist”—an electron-sensitive film into which the pattern for the gratings can be drawn with a beam of electrons. Once the incredibly intricate pattern is drawn, the remaining resist acts as a sort of stencil or mask for the etching process that carves the pattern into the wafer. Etching is done using reactive gases and energy to create a plasma that can cut the pattern into the wafer with atomic resolution.
“The 6,000 or so lines per millimeter on the gratings is relatively easy for our equipment,” said Eichfeld. “The real precision is in the angles of the etched lines, which need to be accurate to the level of the angstrom.”
Penn State’s Nanofabrication Laboratory has many capabilities beyond what McEntaffer uses. The variety of equipment and processes available allow the facility to be incredibly flexible—they work with about half the elements in the periodic table. Processes available at the facility include additive manufacturing, creation of nano-biomechanical systems for personalized healthcare, and materials for free-form electronics and optoelectronics. Penn State faculty and students from fields as diverse as engineering, materials science, medicine, and agriculture make up about 70 percent of the facilities’ users, with the rest coming from other universities and industries.
“Having a facility like this on campus takes down all the barriers to accessing this kind of equipment,” said Eichfeld. “You might need to travel to a national laboratory for this kind of equipment if we didn’t have it here, and that adds time and expense to the process. Just as important though is access to our staff. We meet regularly and consult with users of the facility to help them avoid pitfalls and help them develop cutting-edge processes using the equipment in ways that may have never been done before.”
Collaboration within the college
Once the X-rays are separated into their various wavelengths by the gratings, astronomers need to be able to convert those photons into useful information. Here again, Penn State is a leader in developing detectors, as well as their associated electronics, that have the required precision to gather information from these relatively low-energy X-rays. These detectors can even detect a single X-ray photon.
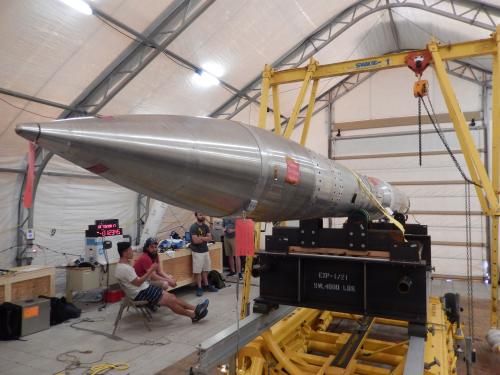
To develop the best possible X-ray spectrographs, McEntaffer works with David Burrows, professor of astronomy and astrophysics, and Abe Falcone, research professor of astronomy and astrophysics. Burrows and Falcone also build instruments to facilitate their research. The hybrid CMOS (complementary metal-oxide semiconductor) detectors that Burrows and Falcone design and build are similar to the sensors in many modern cameras but are much more sensitive and much more precise. They also design incredibly “low-noise” electronics boards, which read out the charge that is generated when an X-ray hits the detector.
“If you think of the amount of electric current that a device typically draws from a standard electrical outlet, the number of electrons owing per second is a one with 19 or 20 zeros behind it,” said Falcone. “When an X-ray hits our detector—depending on its energy—it will produce just a few, or maybe up to a few thousand, electrons through the photoelectric effect in the silicon of the detector. To count the X-rays, our electronics need to be able to read out this incredibly small number of electrons with very low noise.”
The different wavelengths of X-rays that are separated by the gratings in the spectrographs will map to particular pixels on the detectors. The detectors and associated electronics boards are so precise and designed to allow so little background noise that information can be gathered from each individual pixel. This precision allows the researchers to not only detect individual wavelengths of X-rays, but also quantify how much of each is present from a source.
The ultimate test
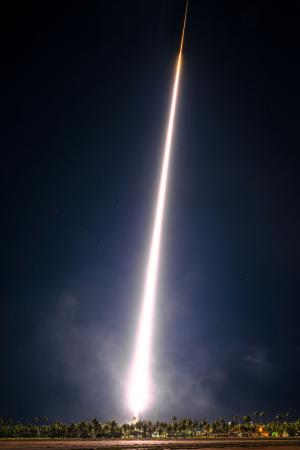
In April of this year, the research team got to put their new X-ray spectrograph to its most rigorous test. The spectrograph was launched on a NASA suborbital sounding rocket. These rockets fly a parabolic path, spending only about five minutes in space, but provide a relatively inexpensive way to ensure that an instrument can do what it’s meant to do and survive being blasted into space on the end of a rocket.
The rocket, launched from Kwajalein Atoll in the Republic of the Marshall Islands, in the Pacific Ocean, is the first-ever NASA sounding rocket mission with a planned water recovery. Most previous astronomical sounding rocket missions were conducted from the White Sands Missile Range in New Mexico and were recovered after landing in the desert. The newly developed water-recovery system will allow missions to be launched in different parts of the world and opens up new parts of the sky that can be the focus of their research.
The X-ray grating spectrograph survived the trip into space and was recovered despite a large hole that breached the hull of the rocket upon reentry. McEntaffer and his group are now processing and interpreting the data collected by the spectrograph, on the Vela supernova remnant in the Milky Way galaxy.
With the success of this mission, the technology has passed another hurdle that will allow it to be a candidate for the next Chandra-or Swift-scale satellite. When that happens, this technology will drive X-ray astronomy for the upcoming decades until another combination of ingenuity, collaboration, and institutional resources—like those that have come together have here at Penn State—can push the technology even further.